RailPro User Group
RailPro => RailPro Specific Help & Discussion => Topic started by: TwinStar on October 26, 2015, 09:09:12 PM
-
I emailed Tim asking for guidance on how to wire in the SoundTraxx CurrentKeeper to an LM-2S. He replied that he doesn't recommend such as it can cause problems. However, he is developing a native Stay Alive capability for RailPro.
Jacob
-
That's good news. I figured he would do that at some point because so many people want it. I'm curious as to how large it will end up being. It seems the Soundtraxx and TCS units are rather large. Trying to fit that in with everything else I have up inside a hood could prove very difficult. However, I think the end result is worth the effort....to have trains that rarely, if ever, loose power would be awesome. I don't have many problems with power loss, but when I do it annoys me.
-Kevin
-
Hopefully the solution, capacitor or battery, comes in several sizes. I'm fortunate to roster mainly E units but cringe at the thought of my GP-7's😁.
Jacob
-
Has their been any updates from Ring on this?
Jacob
-
not that I have heard.
-
not that I have heard.
Maybe I'll nudge Tim with another email.
Thanks.
-
Tim said to check back next month and that something may be available.
-
Sweet!
-
I'm interested in this too!
-
There is no current offering for keep alive from Ring, but the new LM3's do support adding such a device natively.
I have not tried it myself yet, but the LM3 does have inputs for it and it should work with existing K-A technology.
-
There is no current offering for keep alive from Ring, but the new LM3's do support adding such a device natively.
I have not tried it myself yet, but the LM3 does have inputs for it and it should work with existing K-A technology.
Hmmm
-
There is no current offering for keep alive from Ring, but the new LM3's do support adding such a device natively.
I have not tried it myself yet, but the LM3 does have inputs for it and it should work with existing K-A technology.
I emailed Tim today (Monday) to ask for clarification on how to wire a keep-alive/battery to the new LM-3, given it's one new connection (simply labeled "negative" with no explanation). Hopefully he'll send a response tomorrow (Tuesday). I will keep this list informed.
-
I emailed him today asking if it will work with the LM-2's. But, now I'm wondering if there is no such hardware but only the capability with the -3.
Jacob
-
From Tim:
Hi Jacob,
We do not recommend connecting other manufactures products to ours. You could damage either our product or theirs and the worst case would be that you cause a fire. However, at your own risk, you could connect a DCC keep alive to a LM-3 since it has a negative terminal. If the DCC keep alive can withstand track voltage you could connect the most negative wire to the 'negative' terminal on the LM-3 and the positive wire to the blue wire on the 9 pin connector. Connecting to the blue wire will bypass some of the LM-3 internal circuit protection and can cause more damage to the LM-3 if there is an internal short (not likely - but not impossible either).
We do plan to make a RailPro keep alive but it is not expected to be available real soon. We expect our keep alive to work with all RailPro modules (LM-1, LM-2, LM-3).
Please let us know if you have any more questions.
Thank you for contacting Ring Engineering!
-
This morning I received an answer from Tim regarding yesterday's inquiry into wiring the LM-3 to a keep-alive or a battery, and my question about when he thought Ring's keep-alive would be available.
On running on battery:
"To connect a battery to a LM-3 it would be best to connect the negative
battery wire to the 'negative terminal' on the 6 pin connector and the
battery positive to the red wire on the 9 pin connector."
For me at least, since I have a steamer that I plan to run fully on battery power, and given Tim's answer, I think I'll stick with connecting the battery leads to the rail leads (red and black on the 9-pin) and not mess with the new negative lead. That way all I am doing is replacing the DC supply that normally comes through the rails with an onboard DC supply. I get that connecting it according to his suggestion probably eliminates one forward voltage drop (approx 0.65V) across the internal rectifier, but I wonder what else it might bypass (see next quote).
On using an existing DCC keep-alive:
"We do not recommend connecting other manufactures products to ours.
You could damage either our product or theirs and the worst case would be
that you cause a fire. However, at your own risk, you could connect a
DCC keep alive to a LM-3s since it has a negative terminal. If the DCC
keep alive can withstand track voltage you could connect the most
negative wire to the 'negative' terminal on the LM-3 and the positive
wire to the blue wire on the 9 pin connector. Connecting to the blue
wire will bypass some of the LM-3 internal circuit protection and can
cause more damage to the LM-3 if there is an internal short (not likely
- but not impossible either)."
This leads me to the conclusion that I will wait for Ring's keep-alive product. Using theirs, unforeseen problems will be covered by Ring. I can't afford to replace LM-3S modules because I ignored the risks.
And on the subject of Ring's keep-alive:
"We do plan to make a RailPro keep alive but it is not expected to be
available real soon. "
I am bummed that the keep-alive still doesn't have a target release date, and the release of said product seems to be getting pushed off further and further. Any hope I had of it coming out soon is pretty well dashed. But, they say patience is a virtue. Sometimes, I'm not terribly virtuous. ;)
-
Is the desire to attach the keep alive after the module's rectifier, thus necessitating the LM3 ground pin, just to avoid the 0.7V drop of an additional diode? Or is there another reason?
-
RailPro's keep alive will be very cool. Maybe they will just build it into the LM4 and LM4S!
-
Is the desire to attach the keep alive after the module's rectifier, thus necessitating the LM3 ground pin, just to avoid the 0.7V drop of an additional diode? Or is there another reason?
I only mentioned the diode drop in relation to connecting a battery to the module. Tim's suggestion would bypass one of the diodes in the path to the module's internal power supply lines (henceforth referred to as the IPS). I like that because that puts more of the battery's voltage into the module. Since the battery output is only 12vdc, I would like to avoid as much unnecessary loss as possible.
But the keep-alive is to be wired to the 6-pin's new negative lead (the IPS negative line) and the 9-pin's existing blue lead (which is actually the IPS positive line). This actually bypasses the entire rectifier (and according to Tim, any filtering, regulating, and protection circuitry) and as such would avoid a two-diode drop of around 1.3v, but that is not the reason the KA is to be wired that way. The KA must be wired the way Tim instructs because it is polarity-sensitive, so connecting it to the IPS (a point of known, unchanging polarity) is essential. There are other benefits, but that is really the big one.
The following is pure conjecture. Because connecting a KA directly to the module's IPS bypasses the module's internal protection circuitry, I believe the Ring KA will likely have some sort of output protection built in, something I don't believe the DCC KA's have. Which would explain the technical reason for Tim's disclaimer about using DCC KA's at our own risk. Of course, the disclaimer could just be marketing. ;)
-
So avoiding the voltage drop is the only reason. Then the usual KA cap/bridge/resistor setup can be used on the supply lines. Could you add another cell to make the battery 15.7V (+3.70V) and then the diode drop would be just right.
-
Then the usual KA cap/bridge/resistor setup
Can you elaborate on "the usual" please?
-
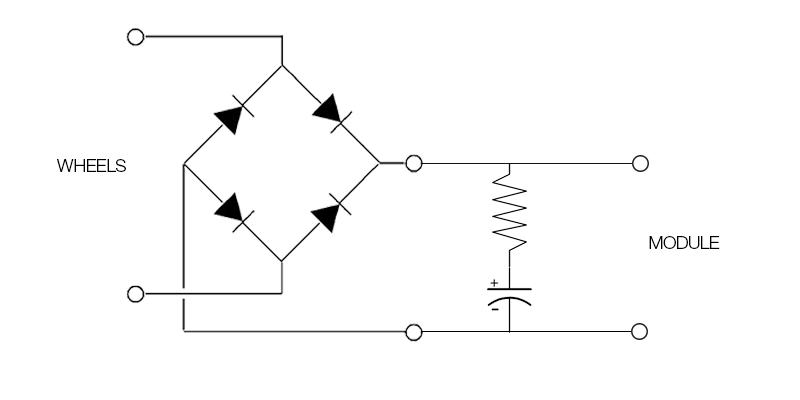
Bridge resolves track polarity issue and prevents capacitor from discharging to the wheels.
Resistor limits capacitor charge/discharge rate.
Capacitor supplies current only when none coming from wheels.
Could eliminate the resistor if not too many locos on the layout. Large amounts of capacitance may make it difficult or impossible to startup the power supply/breakers.
Effectively a filter too so not usable with DCC. Would wipe out the digital packets. This is RailPro. We play with pure steady state DC on the rails. Filter doesn't have anything to filter out.
-
Wouldn't the diode bridge prevent feedback of power from the capacitor to the rails anyway?
Other than using an existing Keep Alive, can you suggest a simple capacitor to use for this?
Or do you really need a bunch of caps to store enough energy for 2 or 3 seconds of travel?
I proposed this some time ago, but never acted on it.
http://model-railroad-hobbyist.com/node/22101
(http://model-railroad-hobbyist.com/sites/model-railroad-hobbyist.com/files/resize/users/Bill%20Brillinger/keep%20alive%20with%20railpro-749x341.JPG)
-
Wouldn't the diode bridge prevent feedback of power from the capacitor to the rails anyway?
Answer
Could eliminate the resistor if not too many locos on the layout. Large amounts of capacitance may make it difficult or impossible to startup the power supply/breakers.
-
Or do you really need a bunch of caps to store enough energy for 2 or 3 seconds of travel?
Yes, you need a lot of capacitance. The advent of low cost super caps make it practical in size. https://en.wikipedia.org/wiki/Supercapacitor (https://en.wikipedia.org/wiki/Supercapacitor)
If you promise not to reverse the track polarity during the test, put a capacitor (correct polarity) across the rails of an isolated section of track. Run the loco. Kill the power. See how far the loco moves. Electrolytic capacitors experience RUD, a SpaceX term ;D, when polarity is reversed. Rapid Unscheduled Disassembly can be very dangerous to you and your train.
-
So avoiding the voltage drop is the only reason. Then the usual KA cap/bridge/resistor setup can be used on the supply lines. Could you add another cell to make the battery 15.7V (+3.70V) and then the diode drop would be just right.
First, I stated, in the case of connecting a KA, that avoiding the drop was NOT the reason to bypass the module's internal rectifier. It is a polarity issue.
Second, yes, you could add an external rectifier and put the KA after it, and then connect that to the red/black rail input wires of the module (as Bill has demonstrated in his post). But then you are introducing yet another 1.3v drop before power ever gets to the module (where if you will recall it has its own internal 1.3v drop). The more voltage you lose, the more you are going to start flirting with under-voltage alarms from the module. For the LM-3 it is best to use the 9-pin blue (+) and 6-pin yellow (-) to connect the KA. I agree that for LM-1's and 2's there is no choice; an external rectifier would be required.
And lastly, I think there is some confusion as to how I am implementing battery power. It is my intention to run the module on battery power exclusively, with no power on the track, AKA dead rail. The battery is not intended to act as a keep-alive. Implementing KA's or Batteries are two very separate issues.
That said, the battery system I'm using is from Dr. Neil Stanton of S-Cab.com. The battery itself is a single cell LiPo 3.7v pack with protection circuitry. It is connected to an S-Cab BPS circuit board, which steps the 3.7v up to 12v. Adding another battery in series to either the existing battery or the BPS output is not an option. 12v is what I have to work with, so if I can save a diode drop here or there I will do so, because I don't want to get under-voltage alarms all the time. The BPS also acts as the charger when a supply is applied through separate charging inputs, and it has all the requisite output current and voltage protection built in.
-
Yeah, I think we have two interspersed conversations going on in this thread - battery power and keep alive.
I get why you don't want additional voltage drop. 12v is marginal to begin with (assuming HO). On the keep alive side of this conversation, there is no real problem implementing without waiting for a new pin on a module providing you start with sufficiently high power supply voltage i.e. power supply other than Ring. Of course Ring is not going to recommend that. No businessman would.
It appears your constraint is the S-Cab board restricting you to a single cell. If you could replicate or find a similar battery management board that works with multiple cells then you wouldn't need post-rectifier ground connection. But that opens up the whole dark side of LiPo so it is totally understandable why S-Cab is single cell.
Even the wall power group suffers from an occasional low voltage warning if your layout is of any size. Our power supplies have no external sense line so wiring inductance causes voltage regulation to be slow and sloppy with lots of over/undershoot. Fortunately, RP seems very forgiving of the condition. I have yet to notice any change in train operation when the warning appears. I think the warning trip is so fast it is catching the ringing in the supply line due to load change. The physical mass of the loco driveline totally masks the voltage swings so the voltage ringing isn't observable in the loco itself.
I installed a ballast load to calm down the ringing. Wasted power as heat but does the job.
(http://www.lkorailroad.com/wp-content/uploads/2016/01/100_7852-768x576.jpg)
Supply rail ringing before:
(http://www.lkorailroad.com/wp-content/uploads/2014/12/wave-1.png)
Supply rail after:
(http://www.lkorailroad.com/wp-content/uploads/2014/12/wave3.png)
-
Anecdotal support:
Years and years ago on a layout far far away I had a helicopter that I wanted to spin up/down realistically. On hand I had four enormous capacitors that had been removed from a broken beefy stereo amplifier. One of those old All Electronics 99 cent gearmotors drove a shaft that went up through the layout to the blades. I put the four huge caps in parallel across the gearmotor terminals and fed 6V through a resistor diode series. Essentially a keep alive all day circuit! :P
The effect was awesome. The caps took so long to charge and discharge with the corresponding slow voltage curve across the gearmotor that the helicopter blades moved very lifelike. It took them several minutes to wind up to speed (or down). A poor man's substitute for pulse width modulation. I wish I had pictures to share but alas it was a time before the luxury of free digital picture taking.
-
1: I get why you don't want additional voltage drop. 12v is marginal to begin with (assuming HO).
2: On the keep alive side of this conversation, there is no real problem implementing without waiting for a new pin on a module providing you start with sufficiently high power supply voltage i.e. power supply other than Ring. Of course Ring is not going to recommend that. No businessman would.
3: It appears your constraint is the S-Cab board restricting you to a single cell. If you could replicate or find a similar battery management board that works with multiple cells then you wouldn't need post-rectifier ground connection. But that opens up the whole dark side of LiPo so it is totally understandable why S-Cab is single cell.
4: Even the wall power group suffers from an occasional low voltage warning if your layout is of any size. Our power supplies have no external sense line so wiring inductance causes voltage regulation to be slow and sloppy with lots of over/undershoot. Fortunately, RP seems very forgiving of the condition. I have yet to notice any change in train operation when the warning appears. I think the warning trip is so fast it is catching the ringing in the supply line due to load change. The physical mass of the loco driveline totally masks the voltage swings so the voltage ringing isn't observable in the loco itself.
5: I installed a ballast load to calm down the ringing. Wasted power as heat but does the job.
1) Yup, HO. I'm still considering, against Tim's advice, connecting the BPS output to the 9-pin blue and 6-pin yellow, but tonight I will be taking some measurements to see what is there under normal conditions. I'm hoping it's reasonably close to 12v. Fingers crossed.
2) I agree, and it may not be a problem even with Ring's PS. I don't know what the output voltage level is so I will be measuring that tonight too. I may be worried for nothing. Trust me, it's happened before.
3) I think I have two options with the BPS. The best option is to contact Dr. Stanton to see if he's willing, on a special order basis, to adjust the converter output to, say, 14 volts. That is unlikely but it never hurts to ask. The other option is to place and external DC-DC converter to step the 12v output to 14v. Problem solved but only if I can fit yet another component inside the engine. Argh!
4) I get low voltage alarms frequently when running trains on a loop of Bachmann EZ-Track. Granted the loop is typically around 60 or 70 feet of track, and they do occur more often at the opposite side of the PS connection, but I do get them. When I have the info screen up I can see the fairly wild fluctuation of the track voltage, almost regardless of where the train is located on the loop. And I agree, the train keeps going, but an alarm I can not clear and just have to wait for it to clear itself is kinda frustrating. Guess it's just my personality.
5) I like it. And your results! Just when I thought terminating resistors were a thing of the past. But actually they are still used to this day on lines like ModBus and DeviceNet and probably many other communication lines. Those resistors can dissipate a considerable amount of power; what resistance are you using?
-
Those resistors can dissipate a considerable amount of power; what resistance are you using?
Ha! Funny you should ask.
They are 20 ohm 100 watt units. At 15V that's about 11 watts of heat. Well within the resistor power rating (25W no heat sink, 100W large heat sink) however after particularly long sessions they get quite hot. In excess of 200 F. I don't like that. So, on the bench right now are replacements - three parallel 100 ohm 100 watt resistors for a net of 33 ohms. At 15V that's about 7 watts but spread over much more aluminum.
The ringing is so well dampened at 0.75A I am banking 0.5A will be good enough. China eBay didn't have 60 ohm available and stateside suppliers want $10 each. I bought a lot of 10 for $28.
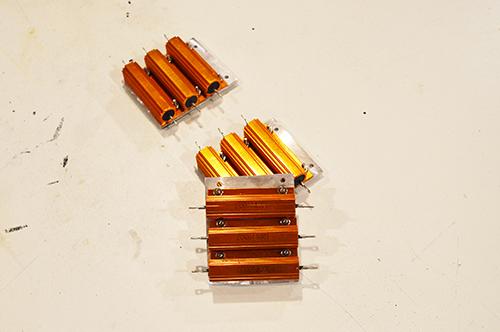
-
Lol, I'm so confused right now. I'm catching bits and pieces but by and large this terminology is way over my head.
-Kevin
-
I"m with Kevin. :-\
-
Wouldn't the diode bridge prevent feedback of power from the capacitor to the rails anyway?
Answer
Could eliminate the resistor if not too many locos on the layout. Large amounts of capacitance may make it difficult or impossible to startup the power supply/breakers.
Sorry Bill. I totally misread your question. My eyes read diode. My brain heard resistor. You must be like Huh???
Yes, the diodes in the bridge rectifier do prevent the capacitor from discharging back to the power supply. So the bridge performs two functions - blocking and polarity rectification.
-
Phew. I thought I was losing it there.
So then for clarity: in light of the diode bridge, the resistor is not needed - correct?
-
So then for clarity: in light of the diode bridge, the resistor is not needed - correct?
For a single loco on the layout the resistor is not needed. As more locos are added to the layout you will eventually reach a point where the combined inrush current of all the caps is so high that the power supply can't startup.
A cap is essentially a dead short at the instant of power up. It's resistance climbs very fast so the "short" is extremely brief. Power supplies are designed to allow excessive current to flow for a very brief moment during power up. If there are a lot of caps then the amount of time that excessive current must flow exceeds the power supply's ability to deliver. Hence, the power supply will shut down. This all happens so fast that it will appear the power supply refuses to turn on. Naturally higher output (amps) power supplies will turn on larger cap loads.
It should be noted that old style iron core transformer power supplies (below) don't suffer from this problem. They will start any cap load or send your wiring up in smoke trying!
-
For a single loco on the layout the resistor is not needed. As more locos are added to the layout you will eventually reach a point where the combined inrush current of all the caps is so high that the power supply can't startup.
Ah! it all makes sense now.
-
Electrolytic capacitors experience RUD
I can attest to that. Way back in high school in electronics class, a fellow student decided to put a cap into a power point (240v) and turn it on. The resulting instant very loud explosion scared the daylights out of everyone and the student was lucky to still have his fingers intact; there was a large dint in the roof where part of the cap hit it.
Anyway this thread is proving most useful with quite a bit of knowledge to be picked up, especially on the dampening of the ringing. Alan, is there a reason why your component values (power dissipation I'm talking about) are so high for this? Back when I was almost a DCC user I did some reading on this and the component values given to do this for DCC wouldn't have handled that amount of power.
- Tim
-
Anyway this thread is proving most useful with quite a bit of knowledge to be picked up, especially on the dampening of the ringing. Alan, is there a reason why your component values (power dissipation I'm talking about) are so high for this? Back when I was almost a DCC user I did some reading on this and the component values given to do this for DCC wouldn't have handled that amount of power.
Because I am using a rude and crude method! :-[ And also because of the difference between DCC and RP DC.
Adding a parasitic load (100W resistors) is a crude way of fixing the problem because it is power wasteful - electricity turned into heat. But, it is the simplest to design, easiest to implement, and has the lowest initial cost. The penalty is a few additional cents on the electric bill!
Relative to DCC...
DCC is an AC square wave on the rails. RP is steady state DC on the rails. This is an extremely important difference. AC buses react somewhat differently than DC buses when a load is applied or removed. While DCC also suffers from load change induced bus ringing, with RP the effect is more pronounced due to it being a DC system. On the flip side, DCC has to deal with all the waveform headaches while RP has no such issues.
Allan Gartner's Wiring for DCC site http://www.wiringfordcc.com/intro2dcc.htm (http://www.wiringfordcc.com/intro2dcc.htm) explains the DCC waveform issues well. To borrow a couple of his images...
DCC waveform at the booster terminals:
(http://www.wiringfordcc.com/atNCEbooster.JPG)
DCC signal 25' from booster:
(http://www.wiringfordcc.com/NCE25ftbus1.JPG)
Closeup:
(http://www.wiringfordcc.com/NCE25ftbusRinging.JPG)
See the ringing in the DCC signal?
I found this trace online that, while not an actual DCC or RP measurement, is a close representation of what you might see if you put DCC and RP on the same scope. The green line = DCC, magenta line = RP. The DCC line rings on the leading and trailing edges of the square wave while the RP line rings when load is changed. Like I said, this is not an actual DCC RP scope trace but I'm hoping a picture is worth a thousand words.
(http://e2e.ti.com/cfs-file/__key/communityserver-discussions-components-files/196/4617.No-DC-Supply-_2D00_-5V-Supply-_2D00_-1000mA-load-_2D00_-no-snubber-on-either-supplies-_2D00_-L7-1_5F00_5uH.png)
It should be mentioned that none of this conversation applies to smaller layouts. Only large layouts, with long runs of wiring and power supplies (or DCC boosters) located large distances away, have to be concerned with ringing. Even then it doesn't seem to be an operational problem for RP, rather it is the fact Tim put that darn warning icon on the controller causing me to investigate further. It bothered me that I went to such trouble building a low voltage drop bus system and still got an occasional warning icon. Had to fix that. >:( Obviously the fix is optional, not mandatory. All other RP layouts are doing fine without it. For my own sanity I had to silence the warning icon.
Wattage-wise:
DCC layouts must accurately control the AC waveform shape in order to work correctly. Long wiring runs, parallel wire paths, and other model railroad realities play havoc on a square waveform. The various components, usually EMI filters and bus terminations, are [may be] added to a DCC track bus to better sharpen the square wave control signal that the layout wiring inductance is otherwise destroying. Minimizing the adverse effects of wiring on the waveform is the reason for many DCC best practices - keep booster distance to a minimum, twist the bus wires, etc. Shaping the AC waveform does not involve large current flow so high wattage components are not needed.
The components I added to my track bus are there to smooth a steady state DC line voltage. My crude method does this by placing a significant load on the line hence high wattage components. Adding new loads on the line (starting a loco) now represent less than 100% of the total current so they have less than 100% effect on the voltage regulation circuitry inside the power supply. Like driving a car with your feet on the brake pedal and accelerator at the same time.
-
Thanks Alan,
I had read Allan Gartner's site. Certainly a recommended site for those in to DCC.
So if I read you correctly, and in basic terms in DCC (AC) you need to "shape the waveform" with filters (resistor and capacitor usually) to dampen the ringing and in DC you need to "control the load" on the line (ballast resistor) to dampen the ringing?
I guess this might be one of the reasons Ring also makes a point about having short buses, "excessive heat generated by large resistors used for dampening at the end of a very long bus might cause a fire" ;)
This is actually good stuff to talk about as some might be contemplating long buses where ringing might become an issue. I know one of the major reasons for dampening the ringing in DCC is to assist in the prevention of the destruction of decoders (the voltage overshoot can and does kill decoders). I wonder if the same ringing issue could be a trap in waiting for us if one was not informed? Your trace back on page 2 showed a peak of about 25v, a significant amount above the max limit of 18v that Ring specifies. I'm sure that Ring has built some margin into it but I wonder?
- Tim
-
So if I read you correctly, and in basic terms in DCC (AC) you need to "shape the waveform" with filters (resistor and capacitor usually) to dampen the ringing and in DC you need to "control the load" on the line (ballast resistor) to dampen the ringing?
There are other methods but basically yes.
I guess this might be one of the reasons Ring also makes a point about having short buses, "excessive heat generated by large resistors used for dampening at the end of a very long bus might cause a fire" ;)
Voltage drop is a common primary concern with long buses as well. Ring may advise against long buses for multiple reasons. The resistors don't reach the ignition temperature of anything found on a model railroad so fire is unlikely but melting styrofoam certainly is possible.
I'm sure that Ring has built some margin into it but I wonder?
During my circuit breaker design and test process I exposed a LM2 to brutal conditions by repeatedly creating dead shorts on the rails with the loco at near stall current draw. I was dialing in my breaker design through trial and err. That one LM2 experienced several hundred shorts on a 15V 5A supply with no dampening whatsoever. It survived without damage and is operating inside a loco on the layout today. A DCC decoder would have checked out after the first couple shorts. LM2 is one tough cookie.
-
"I guess this might be one of the reasons Ring also makes a point about having short buses, "excessive heat generated by large resistors used for dampening at the end of a very long bus might cause a fire" ;)"
So what would be considered a long bus run? I'm going to have a fairly large layout for a home, and will eventually have at least 2 power supplies, possibly 4.
Thanks for this discussion,
Joe
-
My layout has 3 runs of almost 60ft on one PWR56 and I don't have any where that fails the coin test.
-
Voltage drop is a common primary concern with long buses as well. Ring may advise against long buses for multiple reasons. The resistors don't reach the ignition temperature of anything found on a model railroad so fire is unlikely but melting styrofoam certainly is possible.
I know, I was having a bit of a poke of fun at Rings repeated deceleration of "it might cause a fire if it's not our product" in his manuals. I rekon big resistors that can generate a lot of heat would get this warning from Ring.
Voltage drop is the most probable reason for the "short" bus length that Ring advises as the PWR-56 can only take 16AWG wire. I do wish the PWR-56 had bigger terminals; 14 would be better and 12 even more so.
Joe, The PWR-56 manual give a bus length of 30 feet. That can translate into 60 feet (30 feet each way) if your supply is in the middle of the 60 feet but you'd need to make a splitter to do that. Alan might be able to give a better idea of the most practical length you could go to before ringing might become a problem that needs treatment.
- Tim
-
Voltage drop is the most probable reason for the "short" bus length that Ring advises as the PWR-56 can only take 16AWG wire. I do wish the PWR-56 had bigger terminals; 14 would be better and 12 even more so.
I'm sure I'm not the first to think of this, but you can come out of the PWR-56 with a short length (1, 2, 3 inches, whatever you deem necessary) of 16AWG and then either solder it to your 12AWG bus or connect it to a conventional terminal block with your 12AWG bus on the other side.
BTW, if 30 feet is the recommended length for 16AWG, then simple math will show that your 12AWG bus can be approximately 2-1/2 times longer (right close to 76 feet) for the same voltage drop. For large layouts this would seem very beneficial.
(Length of 12AWG bus derived from the ohms per thousand feet rating of both wire sizes.)
-
So what would be considered a long bus run?
That is the $64,000 question for which you will never receive a 100% reliable answer. There are too many variables for one answer to be the right answer everywhere everytime. However, rest assured everyone will ask it! ;D
Because people will ask, manufacturers like Ring attempt to give a single answer that will work 99.99% of the time. That makes the answers very conservative. Look at Bill's situation for instance. Ring says 30' Bill has 60' without problems. Shucks, I have 150' and it works fine. Abiding by artificially low recommendations may place an unnecessary constraint on your construction or dramatically increase your cost. Throwing caution to the wind by totally disregarding electrical design is equally dangerous. At the end of the day, the physical arrangement of your layout space, your appetite for wiring, and your wallet will force certain electrical realities upon you. Fortunately, RP seems to be extremely forgiving. That is a good thing. (to the DCC guys we say neener-neener)
Rather than a single answer it may be better to simply use best practices and let the chips fall where they may in any one situation.
Before I go on I want to say this again - we are talking about large layouts. None of this matters a lick on a smaller railroad. For sake of argument only, let's say a large layout is one where the wire between the power supply and the track is longer than Ring's recommended 30'. And we are talking RP, not DCC.
This much we know for sure - our power systems are effectively this:
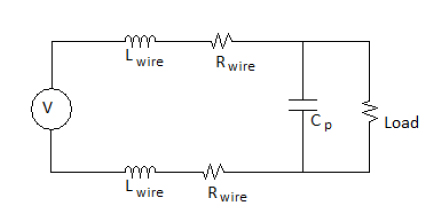
with L = wiring inductance
with R = wiring resistance
with C = wiring capacitance
with V = power supply voltage
with A = load on the circuit (train)
Our goal is to minimize L, R, and C while stabilizing V. Our trains dictate A.
We also know the load on the circuit will vary so it is given L & C will always be in flux.
We also know the voltage regulator in our power supply is >30' from the load so assume regulation will be poor at best. This means not only will L & C change constantly, so will short-time V relative to A.
See how complicated the "right answer" to your question quickly becomes?
Off the cuff shot at best practices:
- (LRC) Use the shortest practical wiring length - route wires in most direct path.
- (LRC) Use the shortest practical wiring length - power supply in middle of wire run instead of at the end.
- (LRC) Use isolated multiple power supplies dispersed around the layout if practical.
- (R) Use the shortest practical effective wiring length - if using one power supply position it electrically central to the layout.
- (R) Use largest practical wire gauge - effective upper limit of 14-12ga as they are the largest readily available economical copper wire sizes.
- (R) Use a lot of short feeders - short <12" small gauge 24-20 to every rail is bulletproof while not being obtrusive trackside.
- (R) Use a feeder for every 3-6' of contiguous rail - refer to ohm's law and the rail resistance of your specific brand track.
- (R) Make high reliability low resistance electrical connections throughout.
- (LC) Avoid parallel wires - Twist bus wires a turn per 1-2'.
- (C) Don't deliberately add capacitance - avoid twisting wires into candy cane tightness.
- (L) Don't deliberately add inductance - avoid small circular wire bundles.
- (C) Limit the charge time of keep alive circuits.
- (V) Possibly add a ballast load at mid-point furthest from power supply - big honkin' resistors. ;D
- (V) Possibly use a power supply(s) with remote sensing.
- (R) The rails are equally part of the power system equation - solder joiners.
The are no doubt many more. My head hurts.
-
At this point, I probably only have about 100' of track laid with only 6 pairs of track feeders. I am using 12 ga bus wire w/18 ga feeder wire, and I make sure all my track joints are electrically sound. I can take voltage measurements anywhere on the layout and get the same reading.
I only have about 1/4 of the potential track laid, but it may be 2-5 years before I am ready for operating sessions.
So much fun, so little time. ;D
Joe
-
At this point, I probably only have about 100' of track laid with only 6 pairs of track feeders. ... I can take voltage measurements anywhere on the layout and get the same reading.
Are you taking the measurements under load? If there is no load on the system then you will always get the same voltage measurements regardless of length.
Place a significant electrical load say an 1156 tail light bulb (= @15V 8 ohms 30W = 2 amps = 4 unit lash-up pulling really hard) on the rails at a feeder point. Measure the voltage at the bulb. Then place the same load 8' away (midway between feeders). Measure voltage at the bulb again. The difference in readings will show you the the effect of wide feeder spacing. Not saying it is a bad thing. Not saying it won't work. Just saying there will be a measurable difference. In the ideal world we want the loaded voltage to be exactly the same everywhere. Closely spaced feeders facilitate this. 16' is pretty wide spacing.
I did the same test on my system except under a load greater than I knew would ever be realistically expected on the rails at any one place. For a load I used an automotive headlight which draws about 4.5 amps @ 15V. The voltage measurements varied slightly from location to location but at worst were only 1.2 volts less than the unloaded power supply voltage of 15.1 volts. I now know that even with a lot of locos in a lash-up pulling really hard they will always receive at least 13.9 volts.
In both cases we are actually measuring the voltage drop of the entire bus and feeder system while under load. Regardless of wire gauge or number of feeders, this is the final answer that matters. It is what your locos will see.
The popular quarter test mentioned earlier is a test to determine if your wiring will allow enough current flow to trip the circuit breaker in the power supply. A good test. But it tells you nothing about what voltage the train will operate from under normal conditions. You really need to know both.
Why you ask? The breaker test is obvious - prevent damage. The voltage test because it feels really good to set the speed of a loco and watch it traverse the entire layout without one iota of speed change. Like your locos to creep at walking pace all the way around without stalling? Keep the voltage even. Ahhhhhh feels so good.
-
Hi Alan, I've taken measurements w/o load, with several engines idling, and with 6 engines pulling a train. The voltage varies a little between testing methods, but the voltage is consistent all around the layout.
The track that I have laid up to this point is mostly permanent, without gaps. At some point I will gap and install feeders at most likely every 6' to facilitate block occupancy detection.
Slow speed control is one thing that I'm really impressed with using the RP system. We use Digitrax at the club and we don't get the same control with the engines there.
Joe
-
Interesting reading.
On a DCC system if you got power from the wheels, ran it through a full wave rectifier, then to a battery, and then to the normal power connections of a LM-2, wouldn't that cover all needs? It could be run as dead rail and would have a built in keep alive on DCC systems.
BTW, did you use heat sink compound between your resisters and the aluminum heat sink?
-
On a DCC system if you got power from the wheels, ran it through a full wave rectifier, then to a battery, and then to the normal power connections of a LM-2, wouldn't that cover all needs? It could be run as dead rail and would have a built in keep alive on DCC systems.
You would need some sort of battery management system to prevent overcharging the battery.
BTW, did you use heat sink compound between your resisters and the aluminum heat sink?
Yes
-
I again had the opportunity to run on a nice Free-mo layout this weekend. While the DCC ran very well the track was still subjected to rapidly becoming dirty. Intermittent interruptions of power and the stalling of the locomotives and restarting of the sound has kept this technology at the top of my want list. I'll be making my desires to Tim known again.
The RailPro ran flawlessly as one would expect. My Broadway Limited EB-7 not so much.